Fasteners and Machining: Necessary Parts for Precision Production
Fasteners and Machining: Necessary Parts for Precision Production
Blog Article
Browsing the Globe of Fasteners and Machining: Methods for Accuracy and Speed
In the detailed realm of bolts and machining, the quest for accuracy and speed is a perpetual obstacle that demands thorough interest to information and tactical preparation. From recognizing the diverse variety of bolt types to choosing optimum materials that can stand up to rigorous demands, each action in the procedure plays a critical function in attaining the desired result. Accuracy machining strategies further raise the intricacy of this craft, calling for a delicate balance between technological knowledge and ingenious strategies. As we explore the techniques that can boost both speed and efficiency in this domain, the interaction in between quality assurance steps and functional quality arises as a critical centerpiece.
Understanding Fastener Types
When choosing fasteners for a project, understanding the different types available is crucial for guaranteeing ideal performance and reliability. Bolts can be found in a vast array of types, each created for certain applications and requirements. Bolts are used with nuts to hold materials with each other, while screws are functional bolts that can be utilized with or without a nut, depending upon the application. Nuts, on the other hand, are inside threaded fasteners that mate with screws or screws, providing a secure hold. Washing machines are vital for distributing the lots of the fastener and preventing damages to the material being attached. Furthermore, rivets are permanent bolts that are optimal for applications where disassembly is not required. Recognizing the differences in between these fastener kinds is important for picking the right one for the task, ensuring that the link is solid, long lasting, and dependable. By picking the suitable bolt type, you can maximize the performance and durability of your project - Fasteners and Machining.
Picking the Right Materials
Comprehending the relevance of selecting the best materials is vital in ensuring the optimal performance and dependability of the picked bolt kinds discussed previously. When it pertains to bolts and machining applications, the product option plays a critical role in establishing the total toughness, sturdiness, rust resistance, and compatibility with the designated setting. Various products supply differing residential properties that can significantly impact the performance of the bolts.
Usual products made use of for bolts consist of steel, stainless-steel, titanium, aluminum, and brass, each having its distinct strengths and weaknesses. Steel is renowned for its high strength and resilience, making it suitable for a wide range of applications. Stainless-steel supplies superb deterioration resistance, perfect for settings susceptible to moisture and chemicals. Aluminum is lightweight and corrosion-resistant, making it appropriate for applications where weight reduction is important. Brass is commonly picked for its visual charm and excellent conductivity. Titanium is recognized for its extraordinary strength-to-weight ratio, making it ideal for high-performance applications. Picking the ideal material involves taking into consideration aspects such as strength needs, ecological conditions, and spending plan restrictions to ensure the wanted performance and longevity of the bolts.
Precision Machining Techniques
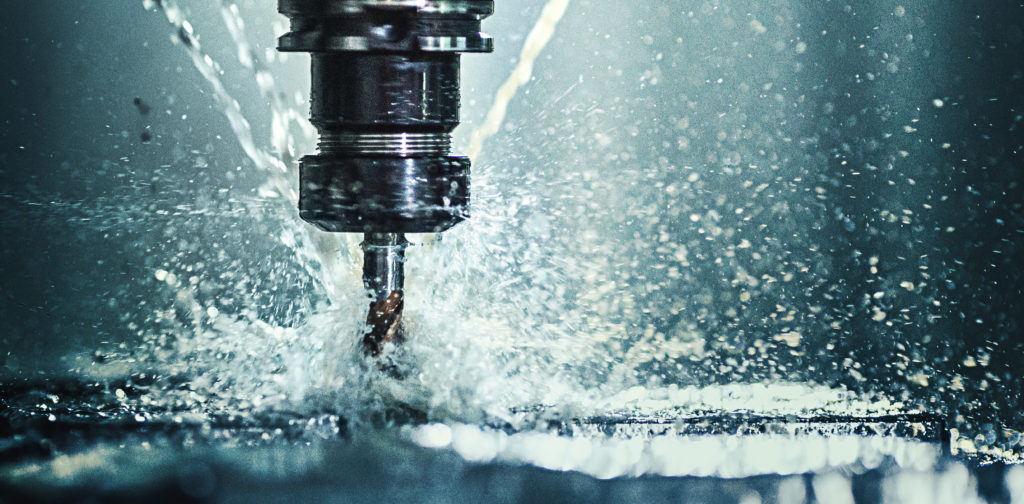
In addition to CNC machining, various other precision methods like grinding, transforming, milling, and boring play essential roles in bolt manufacturing. Grinding helps accomplish great surface coatings and limited dimensional tolerances, while turning is frequently utilized More Bonuses to develop cylindrical elements with specific diameters. Milling and boring procedures are essential for shaping and producing openings in fasteners, ensuring they satisfy specific specifications and function properly.
Enhancing Rate and Efficiency
To optimize bolt production procedures, it is important to streamline operations and implement effective strategies that match precision machining methods. Automated systems can handle repeated jobs with precision and rate, allowing employees to concentrate on more facility and value-added tasks. By combining these methods, manufacturers can accomplish a balance in between rate and precision, ultimately boosting official site their competitive side in the bolt industry.
Top Quality Control Actions
Carrying out extensive quality control actions is important in ensuring the reliability and uniformity of bolt items in the manufacturing process. Quality assurance actions encompass different phases, beginning with the selection of raw products to the last assessment of the finished fasteners. One essential facet of quality assurance is conducting extensive product examinations to verify compliance with specs. This includes examining variables such as product toughness, make-up, and durability to assure that the bolts fulfill sector standards. In addition, checking the machining refines is crucial to promote dimensional precision and surface finish quality. Making use of innovative innovation, such as automatic evaluation systems and precision measuring devices, can improve the accuracy and efficiency of quality assurance treatments.
Routine calibration of tools and machinery is critical to preserve uniformity in production and guarantee that bolts meet the necessary resistances. Implementing rigorous procedures for recognizing and dealing with issues or non-conformities is crucial in protecting against substandard products from going into the marketplace. By developing an extensive quality assurance structure, manufacturers can support the track record of their brand name and deliver fasteners that satisfy the greatest criteria of efficiency and durability.
Final Thought
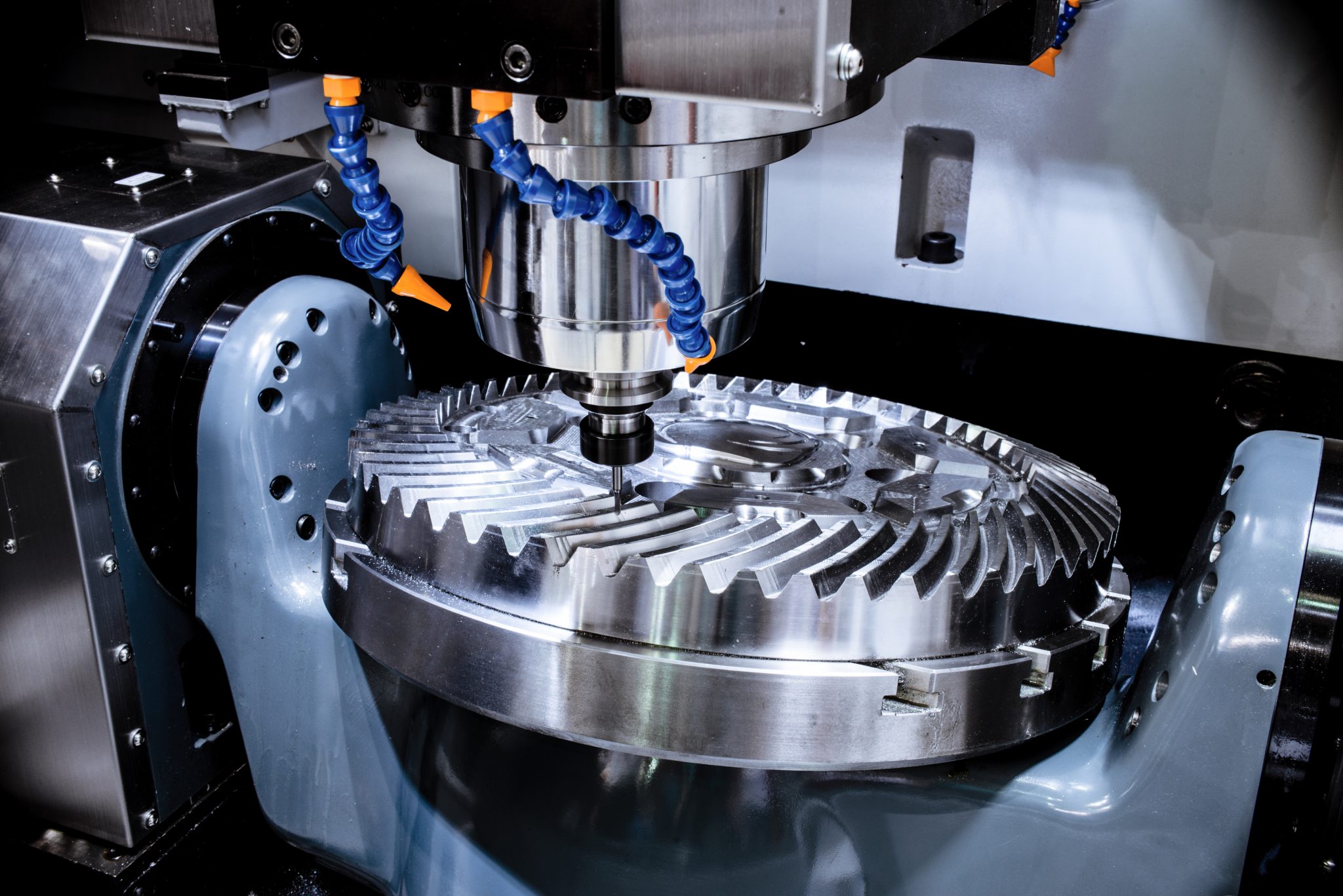
In the complex world of fasteners and machining, the pursuit for accuracy and rate is a continuous obstacle that requires thorough focus to information and critical preparation. When it comes to bolts and machining applications, the product option plays a critical duty in establishing the total toughness, longevity, deterioration resistance, and compatibility with the desired setting. Accuracy machining includes various advanced methods that make certain the limited tolerances and specs required for bolts.In enhancement to CNC machining, other precision strategies like grinding, transforming, milling, and boring play important roles in bolt manufacturing.To enhance fastener manufacturing procedures, it is vital to improve procedures and apply effective methods that match accuracy machining strategies.
Report this page